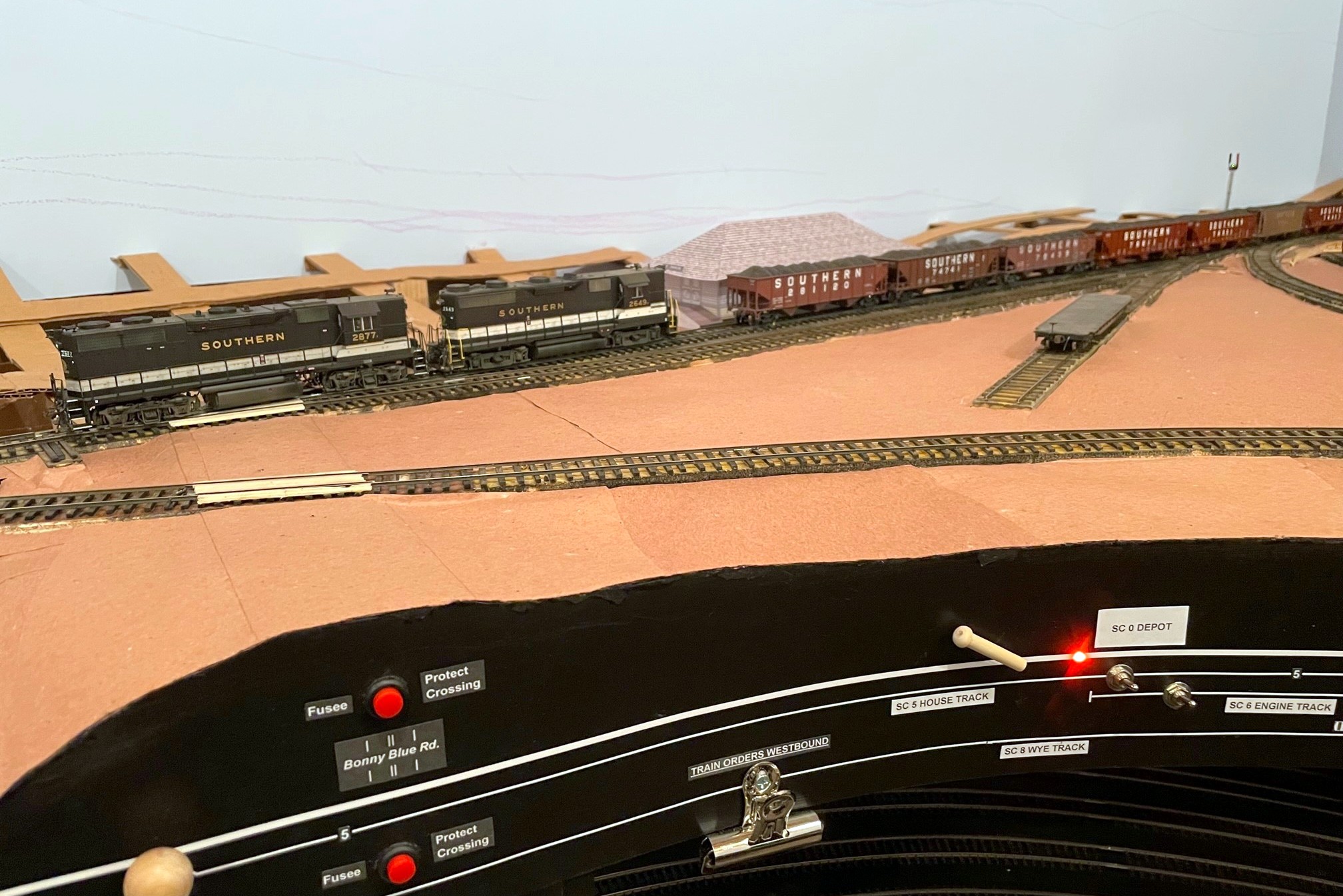
Gravity is a major factor in prototype railroading, but it can be quite troublesome for a model railroad. Very little real track is actually completely flat, so train crews routinely use the handbrakes on individual cars to hold them in place in yards or sidings. Not only do handbrakes hold cars in place, but in the Appalachians where I model, gravity and handbrakes were often used to move cars from empty tracks to tipple loading points, to move loads into the right track below the tipple, or even to run-around a caboose at the end of the line. Modeling working handbrakes on individual cars isn’t very practical, so what is a model railroader to do? Some install springs on the ends of a car’s axles to use friction to hold the car, but this can’t be “turned off” to allow the car to roll freely. Others use little picks they stick into the ballast to hold cars in place, but this can be destructive to scenery, and it leaves an un-prototypical giant stick next to a cut of cars. I’ve adopted a method of fascia-controlled “handbrakes” on the tracks which works well for my needs.
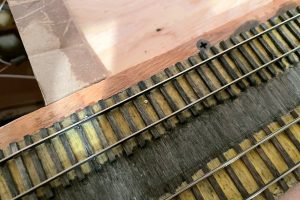
This method is overkill if you just want to hold cars in place on a siding. For this I recommend a drop of CA, a piece of monofilament line sticking up through the tracks, or the end of a soft brush if more strength is needed–I use all of the above for holding cars in place when set out. I use the method here where I need brakes sometimes and free rolling other times, so the first thing you need to do is figure out where you need brakes. I once heard a story about a design presented to a university for a new campus that didn’t show any sidewalks. When the dean of the university asked the designer why there were no sidewalks, the designer replied “wait a year after the campus is open, then you’ll know exactly where the sidewalks need to go based on the trails through the grass.” So, where do I install brakes? Wherever I find I need them when operating trains–a question I also pose to my operators after every session: “is there anywhere you wished you had handbrakes but didn’t.” Generally speaking, they’re needed anywhere a crew will need to leave cars on a grade for a period of time to conduct other work. Since I’ve got lots of grades on the layout, I’ve currently got five handbrakes installed on the lower level alone.
The concept of these fascia-controlled handbrakes is simple: install a movable piece of strong wire between the rails tall enough to hold an axle with a mechanism to retract it when not in use. Once you know about where you need brakes, mark that spot between the rails, and make sure the area underneath is clear enough to install a brake mechanism. Remember, the brake can really be anywhere along a string of cars, so if your ideal spot is not to ideal under the layout or on the fascia, just move it a few inches. I use 1/16″ brass tube as a protective sleeve for the .025″ steel music wire I use as the brake, so once I find a spot, I drill a vertical hole between the ties for the brass rod. I like to offset the rod about 1/4-1/3 between the rails to avoid interfering with truck bolsters (coupler trip pins will also be an issue for those who use them… in fact, a similar mechanism might work for uncoupling too, hmmm…).
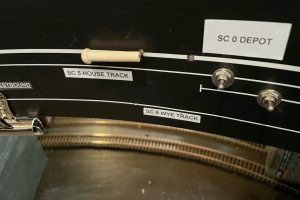
If you’ve followed me for a while, you know I’m a big fan of manual controls using slide switches–I use them for turnout controls, semaphore controls, and now handbrakes. You also know I’m a stickler for creating a fascia where the controls make sense and aid an operator instead of confusing them. In the case of the handbrake, I wanted it to be easy for operators to see when the brake is “set” and when it is retracted, so I settled on a control lever that lies in-line with the track when retracted and sits at a sharp angle when “set.” Just for good measure, I also use a bi-color LED to illuminate amber on the fascia representation of the affected track when the brake is set to help mitigate inadvertently running into a brake with the delicate footboards of a super-detailed locomotive (been there, done that).
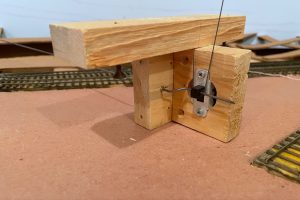
For the brake mechanism, I use a vertically mounted slide switch (DPDT in this case) with a 3/16″ throw–this is just enough to catch the axle of a 36″ wheel in HO scale when extended and still retract to almost rail height when recessed. The brake rod itself is a piece of .025″ music wire bent into a squared-off “J” shape running through a hole in the slide switch–initially, make this piece long enough that it will stick up about 1/2″ or more above the rails when in place. The control mechanism is a piece of thick steel rod (.062″ music wire) with a bell crank bent at one end. Th rod should be cut about 3″ longer than the distance between the brake’s track location and the location of the control on the fascia. The bell crank is offset about 1/4″ from the rod. As you can see in photos, I drill a hole in a piece of 1×3″ board centered on the slide switch and offset about 1/4″ laterally for the control rod to pass through (lined with 3/32″ brass tube for smooth operation). I also bend the bell crank at 45-degree angles instead of 90 as this allows me to make adjustments to the crank offset in either direction, shorter or longer. The structure for the mechanism is typically three boards: 1) the slide switch board with a large hole drilled out for the switch (mounted with screws), 2) the control rod board mounted 90 degrees to the switch where the bell crank is secured, and 3) the attachment board on top to make it easy to mount to the plywood sub-roadbed. I use 1×3″ pine for most of my pieces, but I may use different thicknesses of attachment plates to get the control rod at the right height for the fascia control–the brake wire can be really tall and still work, so better to have the mechanism hanging lower than to have to curve the control rod to the right height. Once I’ve got the three boards assembled with 1 1/4″ drywall screws, I disassemble it, insert the bell crank end of the control rod, insert the bell crank into a hole drilled in the slide switch, adjust the bell crank as needed for smooth operation of the switch, and reattach the boards with the screws.
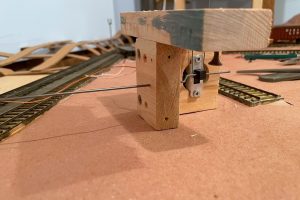
For the fascia, I drill a hole for the 3/32″ brass rod sleeve as close to horizontal as I can get it and pointed directly at the brake location on the track. I pick the spot on the fascia that allows me to do this while keeping the control rod as perpendicular as possible to the fascia (you don’t want the control rod coming out of the fascia at a strange angle if you can help it). The LEDs are nice but not necessary, but this is the step where I drill the holes, about 1″ behind the brake control. I like to drill the hole through the fascia the exact size of the LED bulb and then use a second larger bit from the back side of the fascia to create a space for the rest of the LED–this keeps the LED from popping out the front of the fascia. I use bi-color red/green LEDs which glow a nice reddish amber when hooked up to AC (e.g., DCC track bus), and I attach one lead to one side of the track bus (with a 470K resistor), the other lead to the “up” position of the slide switch, and a third wire from the center position of the slide switch to the other side of the track bus. Super simple.
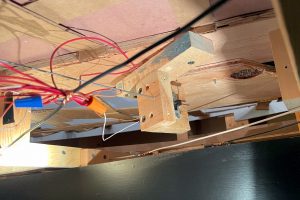
Mounting the switch mechanism is a bit of a pain and requires some planning and patience. From under the layout, I run the control rod through the fascia. Then I find the brass rod going up through the tracks and insert the brake rod (it helps if the brass rod is long enough to protrude beyond the plywood of the sub-roadbed). With the mounting screws on the attachment plate ready to go (screwed in so they’re almost through the board), I gently move the mechanism around until the brake wire is more-or-less vertical, the switch operates freely, and the control rod is as straight as possible between the fascia and mechanism. The mechanism is oriented to put the rod and switch perpendicular to the FASCIA rather than the track (angle relative to track doesn’t matter here). Once I’m happy with the placement, I run the mounting screws into the sub-roadbed.
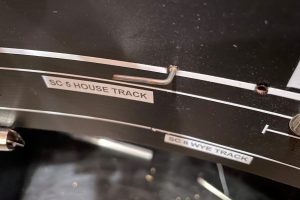
On the fascia side, I now have about 2″ of control rod sticking out. With the slide switch in the DOWN position, I then grasp the control rod with a pair of needle nose pliers flush with the fascia so the bend will be about 3/16″ from the fascia and use my hand to bend the control rod to align with my track diagram (horizontal) in the direction of the bell crank so that “up” on the control = “up” on the brake. My convention is to face the controls and bell cranks to the left, but either works. At this point, I have the leverage to test the mechanism and fix any issues. If all is good, I use a Dremel cut-off wheel to cut the end of the control rod so about 3/4″ beyond the bend. For the control lever, I use a wooden 1 3/8″ “axle peg” which can be found at any large craft store–it’s admittedly an odd shape, but it’s distinct, easy to find, and easy to use. I insert the pegs into a vice and drill a hole the exact size of the control rod about 1″ deep into the center of the peg, then drill another hole in the side about 1/8″ from the flat end into the first hole and use an X-Acto blade to create a notch between the two for the 90-degree bend in the control rod. The peg is usually a press fit onto the control rod.
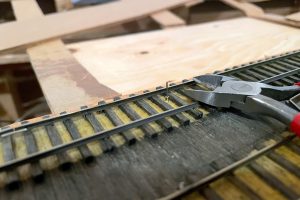
The final step is to trim the brake wire. I’ve found if I use a pair of wire cutters at rail-top level when the brake is in the DOWN (recessed) position, it is low enough for all my locomotives to clear and extends high enough to catch all my axles when needed. Because the wire’s location can be tough to see (especially when cars are over it), I use a little dab of yellow paint on the outside of the rail to indicate where the brake wire lives for easy spotting by crews.
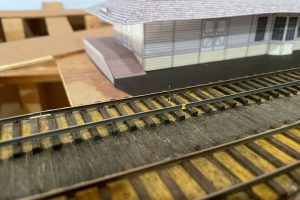
I’ll also share some “lessons learned” for using this type of handbrake:
- The brake will find your lowest-clearance locomotive and keep it from moving until you trim the brake wire–remember this locomotive and use it to test all brake installs
- If you try to pull a string of cars when the brake is engaged, you WILL bowstring every car between the locomotive and the brake off the rails (sometimes violently)
- If you leave the brake “up” and roll cars into it, they will bounce back quite jarringly upon hitting the brake
- If you don’t pay attention and activate the brake under a truck bolster or low-hanging part of the car, you WILL raise the car off the rails and derail it (or topple it)
Other than these “gotchas,” I’m very happy with the operational possibilities these handbrakes add to the model railroad!
Dan, thanks for sharing this method to hold cars I will be using it. I have a project I am working on and hve not yet figured a way of doing it. I am modeling the Pittsburgh Coal Co. 1933 constructed SmithsFerry, Pa. to Negley, Oh. . A 13 mile branch connecting with the Pittsburgh Lisbon & Western RR. The company loaded hoppers via crane from barges to a hopper above the loading track. The cars were pulled ( 4 to 6 } at a time with a cable system that ran on a loop hooks were on the cable that allowed operator to place on loop on hopper car. Cars were loaded as operator pulled them under loader then when done the loading track was on a 2% grade an d dropped to out bound track. I have a DC reversable 1-rpm motor that I plan to use for the cable system I am just trying to devise a way to run said cable fishing line maybe? The cable runs at a angle to get cars from siding to loading track and under loader. this is where my problem is, how not toget line off the main cable tangled around pivot point. And that is my project I am working on now. Thank You Mike